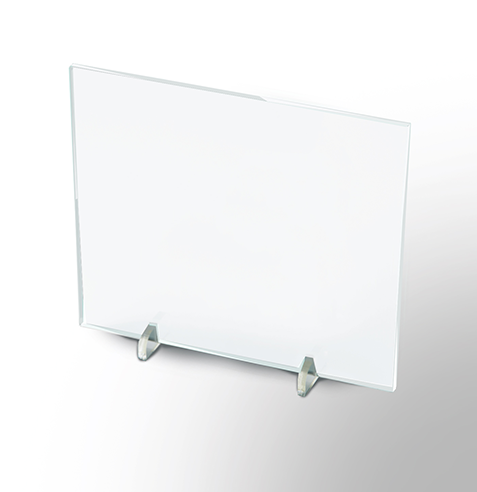
FLOAT GLASS
Float glass is a flat glass product manufactured through a process involving the floating of molten glass on a liquid metal bath, typically tin. This technique yields glass sheets of exceptional flatness and uniformity. The process in the mid-20th century, has revolutionized glass production.
Unlike its predecessors, float glass possesses superior optical properties, allowing for minimal distortion and high light transmission. Its smooth surfaces facilitate further processing, making it a versatile substrate for various applications such as glazing, automotive components, and electronic displays. The inherent qualities of float glass have significantly contributed to advancements in architectural design and technological innovation.
Exceptional Clarity
High Light Transmittance
Durability, Versatility, Sustainability
Recyclability and environmental friendliness
Smooth Surface, Excellent thermal insulation
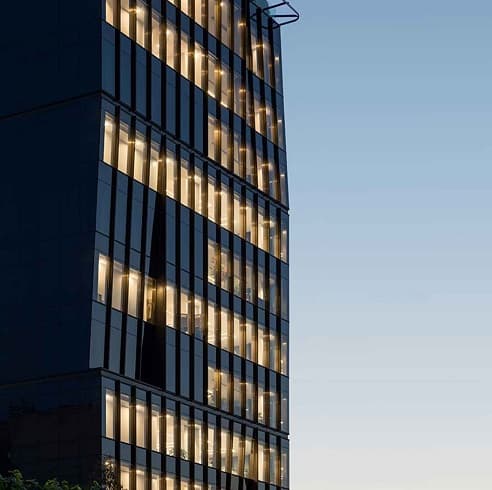
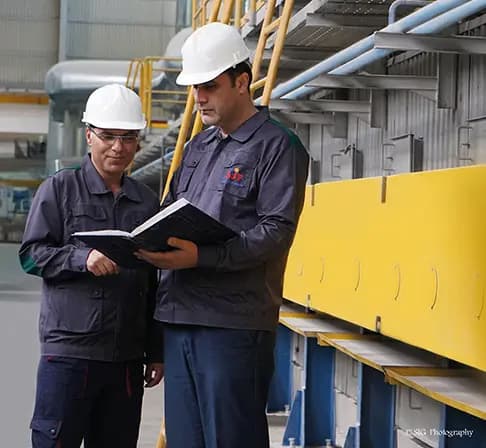
A revolution in Glass Production
The glass manufacturing industry is experiencing a major transformation, fueled by advanced technologies, sustainability demands, and innovative production methods. This shift is redefining how glass is designed, produced, and used across various sectors, including construction, automotive, renewable energy, and consumer electronics. As energy efficiency, environmental impact, and functionality become more important, modern glass production has evolved into a research-driven process, far beyond simply shaping raw materials.
Key advancements by companies like (SIG) include smart glass technologies that adjust transparency and thermal properties . This innovation boosts building energy efficiency, enhances comfort, and lowers costs. Additionally, nanotechnology and coatings have created glass with improved durability, scratch resistance, and self-cleaning features, suitable for high-performance uses.
SIG is also addressing environmental concerns by sustainably sourcing raw materials from renewable or responsibly managed resources. We focus on sustainable mining, low-emission transportation, and efficient production to reduce waste and energy consumption. These efforts ensure SIG’s products support greener, more sustainable manufacturing practices globally.
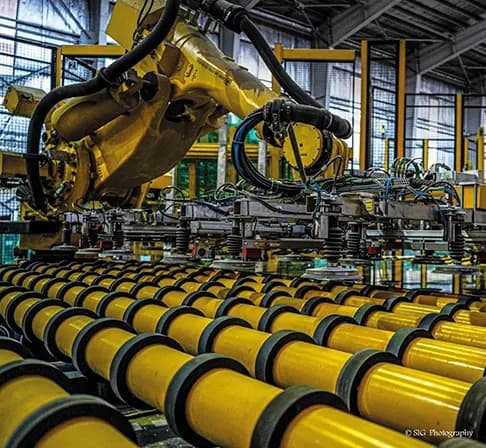
Production Technology and production line of Float Glass
The production of float glass, essential to modern architecture and industry, has seen major advancements, driven by technology and precision engineering. The process involves melting raw materials like silica sand, soda ash, and limestone at high temperatures, allowing the molten glass to float on molten tin. This method creates perfectly flat, uniform glass, which is cooled and annealed for strength and clarity.
Specialist Glass Industries (SIG) has optimized this process with advanced automation and control systems. Their precision engineering ensures high-quality float glass for industries such as construction and automotive. By adopting energy-efficient technologies, SIG has improved production speed and quality while reducing energy use and waste.
SIG’s inspection systems ensure each sheet meets strict standards for clarity and strength. Our focus on innovation and sustainability has made us a National leader not only in technical expertise but also in eco-conscious manufacturing .
Discover What sets SIG apart in Float Glass production
- Geographic Advantage: SIG’s proximity to silica sand reduces costs and supports a sustainable supply chain.
- Focus on Quality: Emphasis on quality suggests strict control and superior production methods.
- Specialization: Being the only glass-specialized industrial town in the Middle East drives innovation and efficiency.
- Global Standards: Commitment to global standards ensures high quality and international competitiveness.
- Diverse Product Basket: Offering various float glass products meets specific market needs and differentiates us.
- Technology Adoption: Leading in new technologies enhances efficiency, reduces waste, and adds unique features.
FAQ
What differentiates float glass from traditional sheet glass?
Traditionally produced sheet glass suffers from thickness variations and surface irregularities, distorting views. Float glass, through a precisely controlled process, achieves exceptional surface flatness and optical clarity, making it superior for most applications.
What is the role of iron content in the color neutrality of clear float glass?
Iron impurities in the raw materials contribute to a greenish tint in glass. Clear float glass utilizes materials with minimal iron content, resulting in a near-colorless appearance for unobstructed views.
How does the float process contribute to the exceptional clarity of float glass?
The float process involves spreading molten glass over a molten tin bath. Surface tension and gravity then act in concert to produce a smooth, polished surface, minimizing optical distortion and maximizing light transmittance.
How does the annealing process enhance the strength and durability of float glass?
Rapid cooling can induce internal stresses within the glass, making it more susceptible to breakage. Annealing involves a controlled cooling process that mitigates these stresses, improving the overall strength and durability of the glass panel.
How does float glass contribute to energy efficiency in buildings?
While clear float glass allows for significant natural light penetration, it can also contribute to heat loss in colder climates. Double or triple-paned insulated glass units (IGUs) utilizing float glass with a low-emissivity (low-e) coating can significantly improve thermal insulation and energy efficiency.